Alkali-Activated Slag,AAS is a hydraulic-cementing material (Slag and fly ash have potential activity), with dry granulated blast furnace Slag as the main raw material, with appropriate amount of silicate cement clinker, a small amount of dihydrate gypsum, and an appropriate amount of Alkali activator, consisting of 80%~85% Slag, 5%~10% Alkali activator, and cement clinker. Alkali-activated cementitious material is not only an energy-saving and environment-friendly building material, but also has superior mechanical properties and durability, and relatively low price. It is a kind of green environment-friendly cement and one of the hot spots in the field of building materials research.
Key Point
The hydration products and structure of alkali-activated cement are greatly affected by alkali components, and different hydration products and structures will produce different carbonation behaviors, which makes the carbonation process of alkali-activated cement become particularly complex. At present, there are many researches on alkali-activated cement carbonation reaction rate and mechanism at home and abroad, but less attention has been paid to the evolution of AAS’s microscopic pore structure after carbonation. So the accelerated carbonation under alkali – stimulate the carbonization process of slag cement mortar, analysis of its internal pore structure evolution law, the carbonization mechanism of study of AAS, improve alkali – inspire slag cement mortar, concrete carbonation resistance and the comprehensive evaluation of alkali – stimulate the durability of slag cement concrete has the realistic meaning and engineering value.
01 Test material
The glass abrasive blast furnace slag and P.I 42.5 Portland cement produced by a certain iron and steel company were used in the test. The main chemical components of slag and cement were determined by X-ray fluorescence, as shown in the table below.
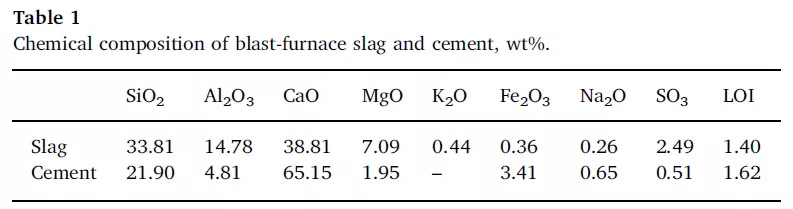
The particle size distribution of selected materials was determined by laser particle size analyzer, as shown in the figure below.
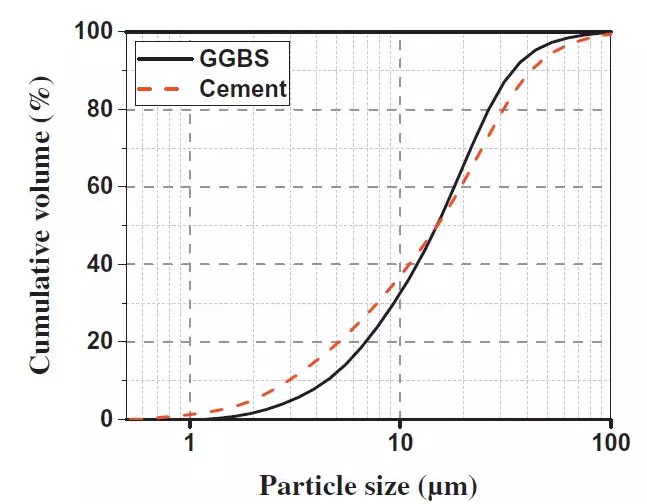
FIG. 1 Particle size distribution of GGBS and cement
In addition, river sand with the maximum particle size of 2.36mm, fineness modulus of 2.75 and apparent density of 2530kg/m3 was used to prepare mortar samples. Industrial-grade granular NaOH (purity: 99 1%) and sodium silicate solution were selected as basic activators (main components: 8.3% Na2O, 26.5% SiO2 and 65.2% H2O).The alkaline activator solutions with 0, 0.5, 1.0 and 1.5 molar mods (SiO2/Na2O molar ratio) were prepared 24h before the formal start of the test.
02 Mix ratio and sample preparation
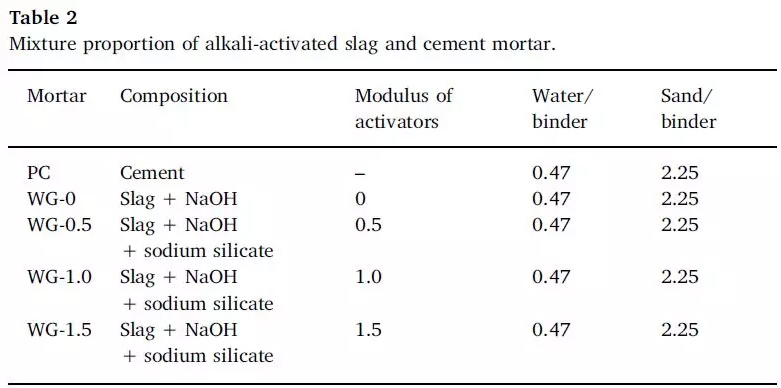
FIG. 2 Mixing ratio grouping of alkali-activated slag sample and cement mortar sample
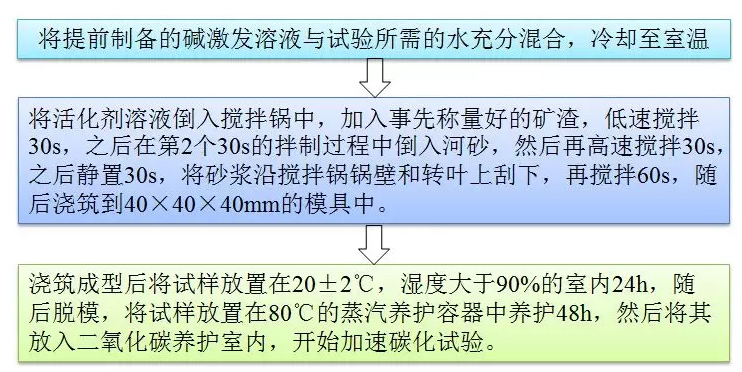
FIG. 3 Flow chart of sample preparation
03 Microscopic pore structure detection
In order to describe the changes of micropore structure before and after carbonization of PC and AAS mortar, MacroMR12-150H-I low-field nuclear magnetic resonance analysis system was adopted, and 40*40*40mm mortar samples before and after carbonization were tested by nuclear magnetic resonance. First, put the sample at 60 °C in the oven for 24h. And then cooled to room temperature (20 °C), using vacuum saturation device make mortar samples saturated.
Results
01 The influence of carbonization on the compressive strength of samples
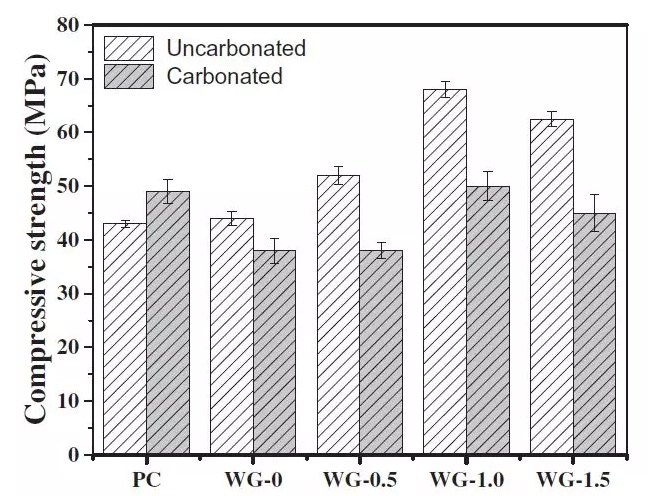
FIG. 4 Compressive strength of AAS and PC mortars before and after carbonization
It can be seen from the diagram that, the compressive strength of concrete carbonation make PC, this is mainly due to the carbonation in cement hydration products of secondary reaction, generated by the tiny crystals, can fill the pores in the matrix, reduce pore, play a role in solid, so that the compressive strength increased.
On the contrary, for alkali-activated slag cement mortar, carbonation reduces the compressive strength of samples at different concentrations. At present, it is mainly explained from the following two aspects: first, the low crystallization rate of calcium carbonate in the carbonization process is related to the low crystallization rate of calcium carbonate. In the hardened alkali active slag, the low Ca/Si of C-S-H can inhibit the formation of CaCO3.The second theory holds that, despite the low Ca/Si of high durability C-SH gel, once decalcification occurs, the damage of C-S-H gel is faster and the gel cohesion is reduced.
02 Effects of carbonization on porosity of samples
The effects of carbonization on the porosity of AAS and PC samples before and after carbonization were studied with volume change, dry sample signal and porosity. See table 3 for details.
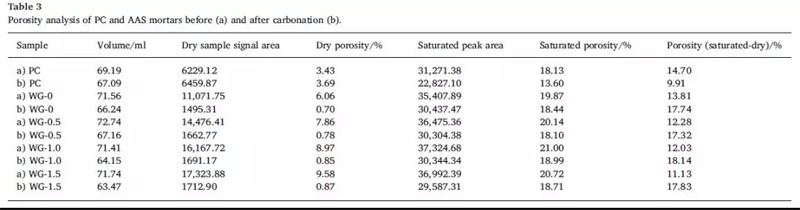
It can be seen that the volume, dry sample signal and porosity of PC and AAS were significantly different before and after carbonization. The results show that the shrinkage effect of carbonization process on all samples, but the shrinkage rate of PC samples is low. This is mainly related to the transformation of Ca(OH)2 expansion into CaCO3. Studies have shown that the formation of calcium carbonate increases the volume by 11.8%. On the other hand, when the modulus of 0, 0.5, 1 and 1.5 is adopted, the shrinkage rate increases by 7.43%, 7.67%, 9.98% and 11.53% respectively with the increase of the modulus of water glass. This may be because the formation of C-S-H inhibits the crystallization of calcium carbonate as the modulus of the sodium silicate increases. In addition, the formation of hydrotalcite during carbonization may also interfere with the crystallization of calcium carbonate.
03 Effect of carbonization on pore structure of samples
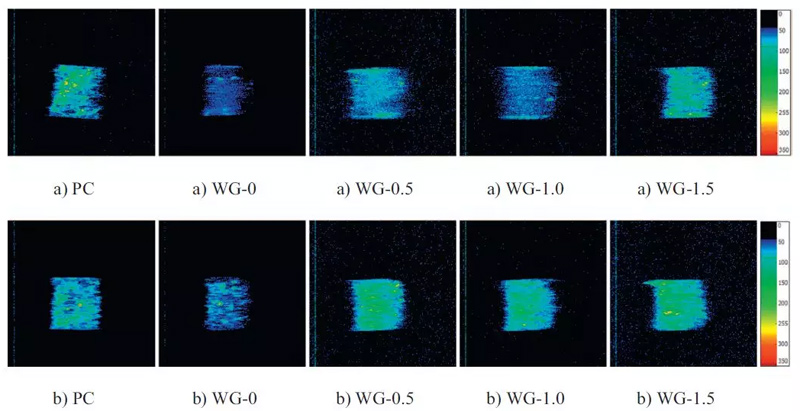
FIG. 5 NMRI images of mortars before (a) and after carbonization (b)
Magnetic Resonance Image
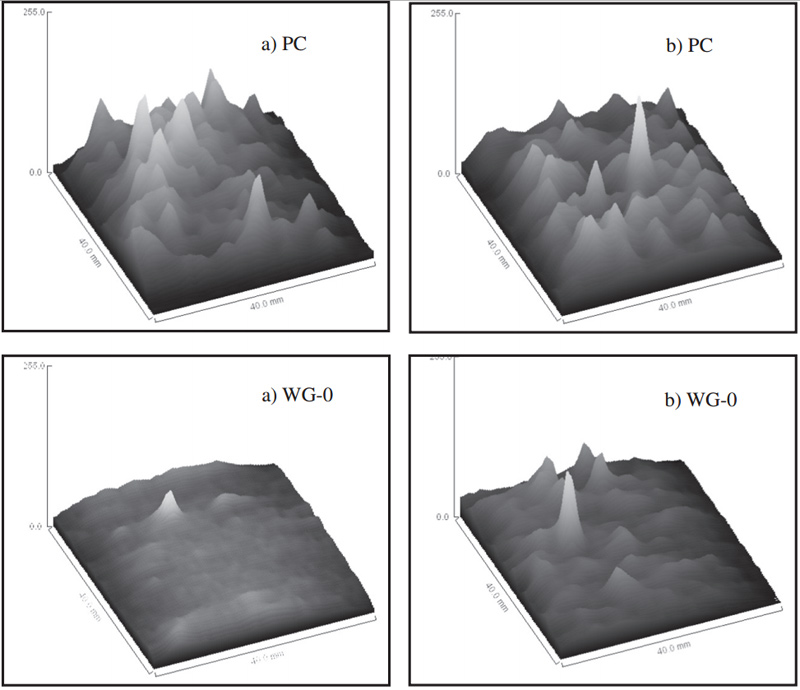
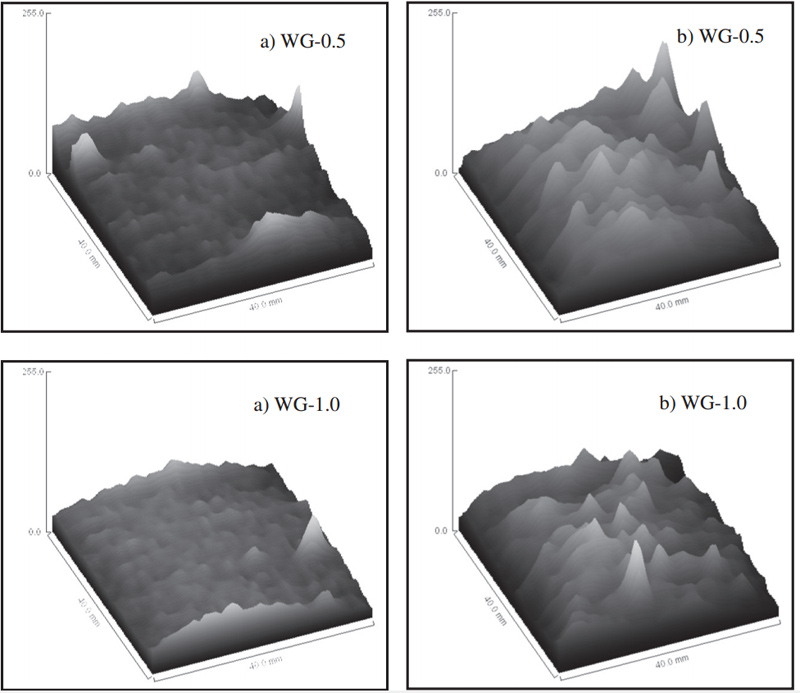
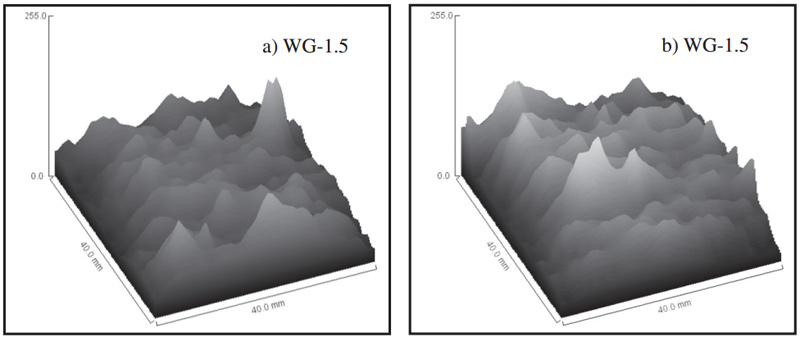
Fig. 6 Gray value of MRI images of motars before (a) and after carbonization (b)
06 Effect of carbonization on transverse relaxation time of NMR
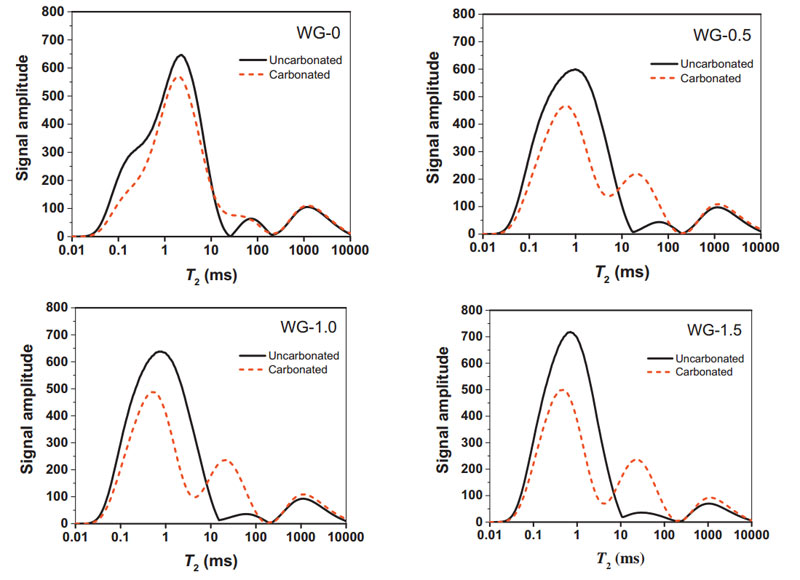
FIG. 7 Change characteristics of T2 spectrum of samples before and after carbonization at various AAS concentrations
As can be seen from the figure above, the T2 graph curve of the pores of alkally-activated slag cement mortar changed significantly before and after carbonization. After carbonization, the number of small pores in the sample decreased, and the number of medium and large pores increased to a certain extent. The pore size distribution of AAS and PC samples is basically the same on a large scale. The span of pore distribution in each matrix is caused by the difference of product density.
Results
1) Carbonation has an adverse effect on the compressive strength of alkali-activated slag cement mortar (concrete).
(2) Compared with pure NaOH solution, with the increase of sodium silicate modulus, c-s-h was transformed into a phase with lower Ca/Si, and the compressive strength of the sample was higher. In AAS samples, especially in the presence of sodium silicate, c-s-h is more likely to precipitate calcium.
(3) Based on the low-field NMR technology, the change characteristics of microstructure of PC and AAS samples before and after accelerated carbonization can be intuitively and clearly analyzed, providing a new way to further explore the evolution law of internal pore structure of samples under accelerated carbonization.